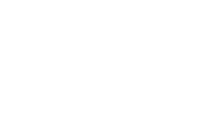
MP3Juice Free Downloads
In the digital era, accessing music has become easier than ever before. Yet, the costs associated with streaming services can be a barrier for many music enthusiasts. MP3Juice offers a seamless solution by providing free access to a wide range of music downloads. This comprehensive guide will delve into the various aspects of MP3Juice, from its easy-to-use interface and vast music library to navigating the platform safely and responsibly.
Introduction to MP3Juice
MP3Juice is a premier online platform that enables users to freely download a multitude of songs across various genres. This service caters to music lovers who seek a no-cost solution to build their music collections. MP3Juice stands out in the crowded field of music services with its user-friendly design and a robust selection of music.
What Sets MP3Juice Apart?
- Extensive Music Library: Users can explore an array of genres, discovering everything from global hits to obscure tracks.
- High-Quality Audio: MP3Juice ensures that all downloads are available in the best possible audio quality.
- Ease of Use: The platform's straightforward interface makes finding and downloading music a breeze.
- Completely Free: Unlike many streaming services, MP3Juice requires no subscription or payment.
How to Use MP3Juice
Using MP3Juice is remarkably straightforward, designed to ensure that even users with minimal technical skills can navigate the platform with ease. Here’s how to get started:
Step-by-Step Guide to Downloading Music
- Navigating the Platform: Open your web browser and visit the MP3Juice website.
- Searching for Music: Utilize the search bar to type in the name of the artist, track, or album you’re interested in.
- Downloading Tracks: Once you locate your desired track, click the download button to save it to your device.
Pro Tips for a Better Experience
- Specific Search Terms: Use detailed search queries to find your music more quickly and accurately.
- Preview the Tracks: If available, listen to a snippet of the track to ensure it meets your expectations before downloading.
Benefits of Using MP3Juice
The advantages of using MP3Juice extend beyond just free music downloads. Here’s what you can expect:
Unlimited Access to Diverse Music
Enjoy unrestricted access to MP3Juice’s extensive library, where you can explore new music without the worry of incurring costs associated with premium services.
Discover New Artists and Genres
MP3Juice is an excellent platform for music discovery, offering users the chance to explore different musical styles and artists from around the world.
Navigating Legal and Ethical Considerations
While MP3Juice offers an attractive service for downloading music for free, it is crucial to approach its use with an understanding of the legal and ethical implications.
Understanding Copyright and Responsibility
It's important to be aware of copyright laws in your region and ensure that your use of MP3Juice complies with these laws. Always strive to use the platform in a manner that respects the rights of artists and creators.
Supporting Artists
Consider supporting artists in other ways, such as purchasing their music or merchandise, or attending live concerts. This helps ensure that artists are compensated for their work, contributing to the sustainability of the music industry.
The Future of Music Downloads
As the digital landscape evolves, MP3Juice continues to adapt, ensuring it remains at the forefront of the music download industry by integrating user feedback and technological advancements.
Anticipated Innovations
Looking forward, MP3Juice aims to enhance user experience through improved functionality, including smarter search capabilities, personalized music recommendations based on user preferences, and a more streamlined interface.
Conclusion: Embrace the Power of Free Music Downloads
MP3Juice is more than just a music download site; it's a comprehensive platform that empowers users to access a wealth of music without financial barriers. By providing high-quality downloads and an easy-to-use interface, MP3Juice is helping to democratize music access worldwide.
The Cultural Impact of MP3Juice
The impact of MP3Juice extends beyond individual users. By making music more accessible, it promotes cultural exchange and broadens the appreciation of diverse musical genres, enriching the global music culture.